Di bidang fasilitas industri dan komersial, efisiensi dan keandalan sistem pendingin merupakan landasan untuk menjaga lingkungan kerja yang optimal. Pendingin memainkan peran penting dalam pengaturan suhu, melayani beragam aplikasi mulai dari sistem HVAC hingga proses industri. Namun, pengoperasiannya yang lancar bergantung pada manajemen proaktif, pemeliharaan yang ketat, dan perencanaan strategis.
Penyebab Umum Kegagalan Chiller:
1. Kebocoran Refrigeran:
Penyebab: Korosi, getaran, atau pemasangan yang buruk dapat menyebabkan kebocoran zat pendingin.
Pencegahan: Periksa dan pelihara saluran, sambungan, dan komponen zat pendingin secara teratur.
2.Skala dan Pengotoran:
Penyebab: Akumulasi kerak, kotoran, atau kontaminan lainnya pada permukaan penukar panas.
Pencegahan: Terapkan jadwal pemeliharaan rutin untuk pembersihan dan pengolahan air.
3. Masalah Kompresor:
Penyebab: Kelebihan beban, masalah kelistrikan, atau kegagalan mekanis pada kompresor.
Pencegahan: Pantau kondisi pengoperasian secara teratur, lakukan pemeliharaan preventif, dan pastikan pelumasan yang tepat.
4. Kegagalan Listrik:
Penyebab: Komponen kelistrikan, sambungan, atau masalah catu daya rusak.
Pencegahan: Periksa dan uji komponen, sambungan, dan sistem kontrol kelistrikan secara teratur.
5. Biaya Refrigeran Tidak Memadai:
Penyebab: Pengisian daya yang salah saat pemasangan atau kebocoran zat pendingin.
Pencegahan: Lakukan pengisian zat pendingin secara akurat selama pemasangan dan lakukan pemeriksaan kebocoran secara berkala.
Tindakan Pencegahan untuk Meminimalkan Waktu Henti:
1. Perawatan Rutin: Tetapkan jadwal perawatan terperinci yang mencakup tugas harian, mingguan, bulanan, dan tahunan. Periksa dan bersihkan koil kondensor dan evaporator secara teratur, periksa level zat pendingin, dan kalibrasi sensor. Ganti komponen yang aus, seperti sabuk dan filter, sebagai bagian dari perawatan rutin. Pertimbangkan untuk menerapkan sistem manajemen pemeliharaan terkomputerisasi (CMMS) untuk penjadwalan dan pelacakan yang efisien.
2. Pengolahan Air: Kembangkan rencana pengolahan air komprehensif yang mengatasi masalah kualitas air spesifik untuk lokasi geografis Anda. Lakukan pengujian air rutin untuk menilai tingkat pH, kekerasan, dan kandungan mikroba. Terapkan kombinasi perawatan kimia, seperti penghambat korosi dan biosida, yang disesuaikan dengan kebutuhan sistem pendingin. Berkolaborasi dengan spesialis pengolahan air untuk menyesuaikan program yang selaras dengan kebutuhan unik fasilitas Anda.
3.Pemantauan dan Analisis: Pasang sistem pemantauan canggih yang dilengkapi dengan sensor, pencatat data, dan alat analisis waktu nyata. Manfaatkan algoritme pembelajaran mesin untuk menganalisis data historis dan memprediksi potensi kegagalan. Menerapkan kemampuan pemantauan jarak jauh untuk memungkinkan analisis di luar lokasi dan respons cepat terhadap alarm. Integrasikan sistem pemantauan dengan pusat kendali terpusat untuk pengawasan komprehensif dan pengambilan keputusan cepat.
4. Deteksi Kebocoran Refrigeran: Gunakan teknologi pendeteksi kebocoran zat pendingin yang canggih, seperti sensor inframerah atau detektor ultrasonik, untuk menentukan kebocoran secara akurat. Terapkan jadwal pengujian kebocoran secara berkala, termasuk metode deteksi kebocoran elektronik. Tetapkan protokol untuk respons cepat, yang melibatkan personel terlatih yang dilengkapi dengan peralatan dan perlengkapan keselamatan yang sesuai. Perbarui peralatan pendeteksi kebocoran secara berkala untuk memanfaatkan kemajuan teknologi terkini.
5.Pelatihan dan Dokumentasi: Melembagakan program pelatihan komprehensif yang tidak hanya mencakup prosedur pemeliharaan rutin tetapi juga protokol tanggap darurat. Buat dokumentasi terperinci, termasuk panduan pemecahan masalah, log riwayat peralatan, dan manual pemeliharaan. Kembangkan gudang pengetahuan online yang dapat diakses oleh staf pemeliharaan untuk pembelajaran berkelanjutan. Mengadakan sesi pelatihan rutin dan forum berbagi pengetahuan untuk meningkatkan keterampilan personel pemeliharaan.
6. Pengoptimalan Beban: Menerapkan strategi pengoptimalan beban dinamis yang memanfaatkan teknologi kontrol terbaru. Memanfaatkan penggerak berkecepatan variabel untuk memodulasi keluaran chiller berdasarkan permintaan waktu nyata. Integrasikan algoritme kontrol cerdas yang menyesuaikan titik setel dan parameter pengoperasian secara dinamis. Lakukan audit energi secara rutin untuk menyempurnakan strategi optimalisasi beban demi efisiensi puncak. Berkolaborasi dengan produsen sistem kontrol untuk menerapkan fitur manajemen beban terbaru.
Pendingin Industri Semi Hermetik
Pendingin Industri Semi Hermetik
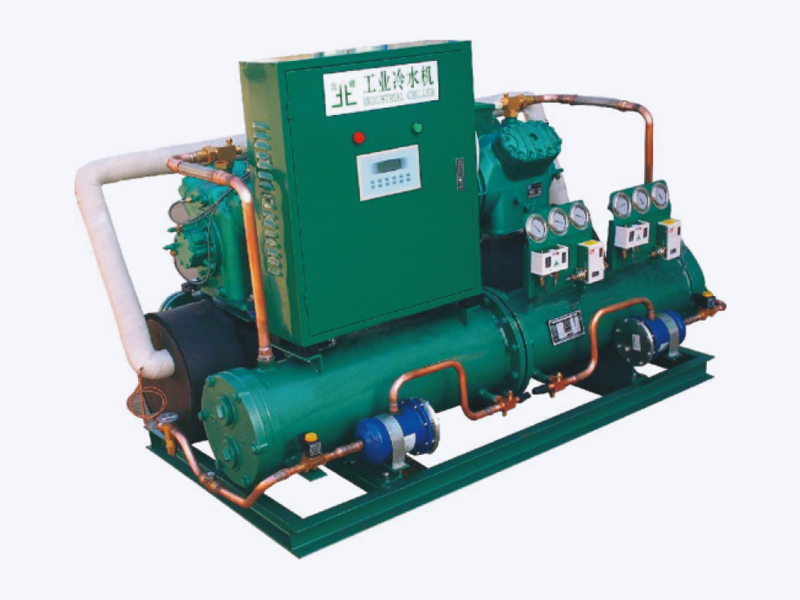